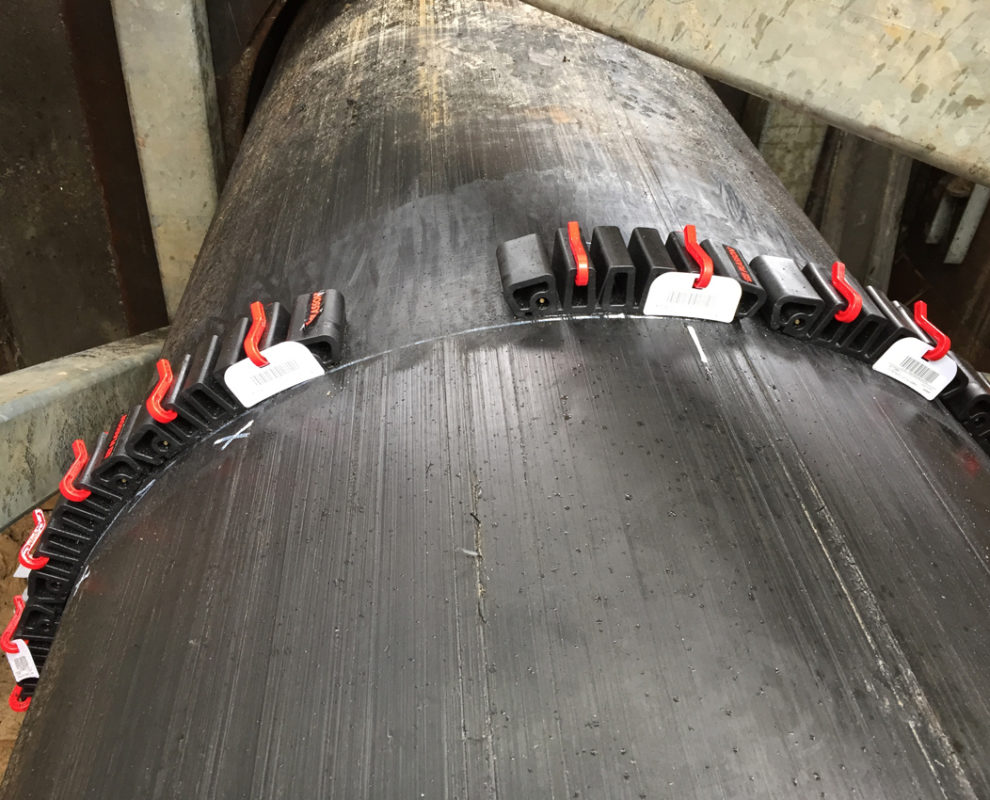
Close-Fit-Verfahren werden seit Jahren erfolgreich zur Rehabilitation von Gas- und Wasserrohrleitungen bzw. zur Renovierung von druck- und drucklosen Abwasserleitungen und -kanälen eingesetzt. Die Close-Fit-Technik besteht im Wesentlichen darin, z.B. thermoplastische Kunststoffrohre aus Polyethylen durch Reduktion oder Verformung im Querschnitt zu reduzieren, um sie anschließend in das schadhafte Altrohr einzuziehen. Dabei wird der sogenannte werkstoffeigene „Memory-Effekt“ von Polyethylen genutzt, um die Rohre nach dem Einzug wieder in ihre ursprüngliche kreisrunde Form rückzuformen.
Durch einen kontrollierten Installationsprozess bei einer verfahrensabhängigen Rückverformung legt sich das neue Rohr „close fit“ also sehr eng und ohne Ringraum an das Altrohr an. Der Einzug des PE-Rohrstrangs findet dabei über die vorhandenen Schachtbauwerke (z.B. bei drucklosen Abwasserkanälen) bzw. kleine Start- und Zielbaugruben (in der Regel bei Druckrohrleitungen) statt. Im Ergebnis wird ein PE-Reliningrohr mit der Qualität und der zu erwartenden Lebensdauer eines Neurohres eingezogen. Je nach Verfahren sind Einbaulängen von mehreren hundert Metern und Dimensionen von bis zu 1600 mm realisierbar.
Festpunkte verhindern Rohrbewegungen
Um ein Verschieben der Rohrleitung oder Bewegungen der Rohrleitung in jeglicher Richtung auszuschließen, muss diese in Ihrer Position fixiert werden. Insbesondere beim Rohreinzug wirken Kräfte in Zugrichtung, die Längsspannungen im PE-Rohr verursachen, die sich auch noch nach dem Einzug und der erfolgten Rückverformung sukzessiv abbauen. Zudem gilt es die temperaturabhängige Längenänderung des PE-Rohres zu berücksichtigen. Diese führt dazu, dass das PE-Rohr in Abhängigkeit seiner Temperatur bei Lagerung, Einbau oder im Leitungsbetrieb länger oder kürzer werden kann. Bei Druckrohrleitungen ist darüber hinaus auch eine Längenänderung durch Innendruckbelastung zu berücksichtigen. Es entstehen Spannungen im Rohr und daraus resultierende Zug- und Druckkräfte müssen durch konstruktive Maßnahmen aufgenommen werden.
Im Ergebnis wird sichergestellt, dass sich das neue Rohr nicht in das Altrohr zurückzieht oder z.B. an das neue Hauptrohr angebundene Anschlüsse und weitere Rohrverbindungen nicht abscheren. Vor diesem Hintergrund kommt der Installation von Festpunkten eine besonders wichtige Bedeutung zu. Mit dem PLASSON Flex-Fixierblock steht dem Anwender ein universell einsetzbarer Festpunkt als Elektroschweißformteil mit definierter Kraftaufnahme zur Verfügung, um die längskraftschlüssige Ausbildung von Close-Fit-Linern und/oder Anschlüssen einfach, schnell und innerhalb eines großen Rohrdimensionsbereiches sicherzustellen (Bild 1).
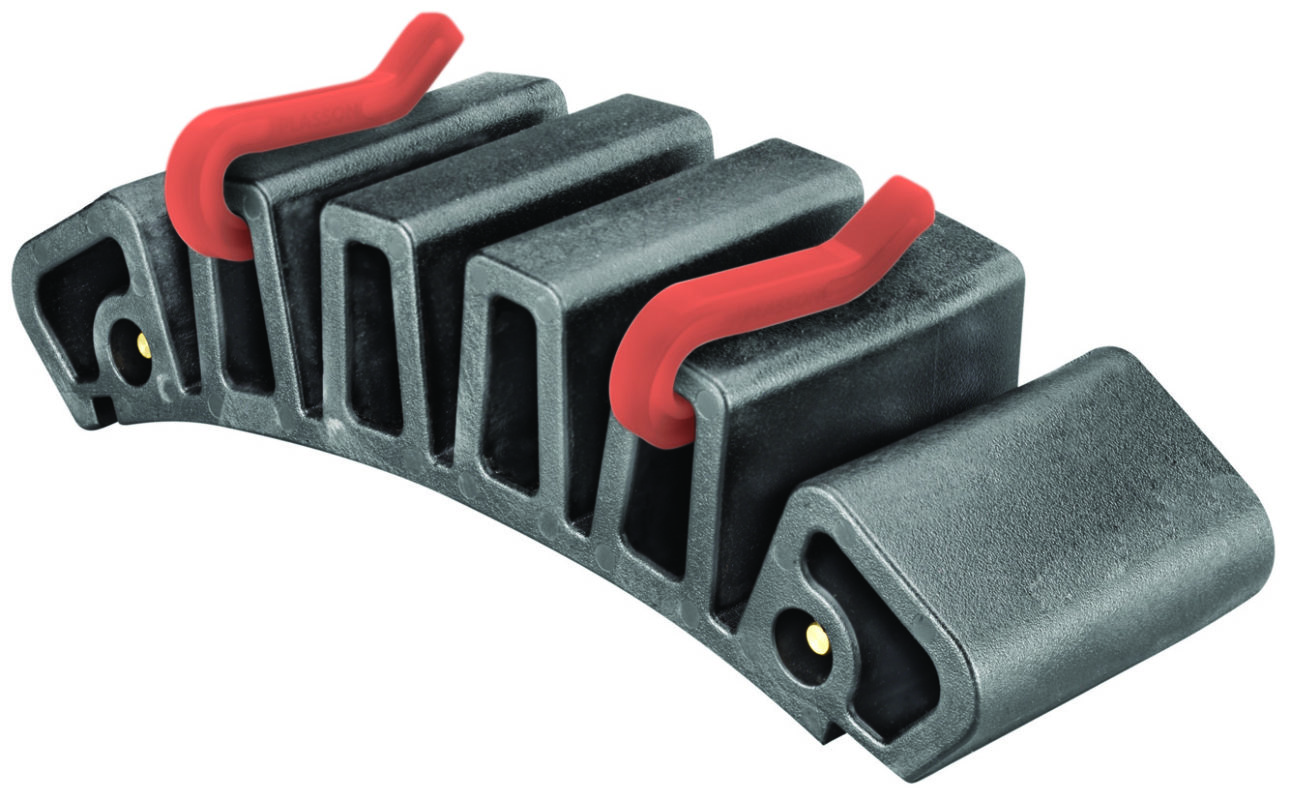
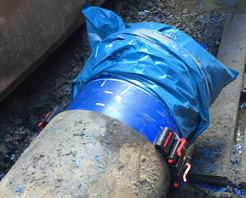
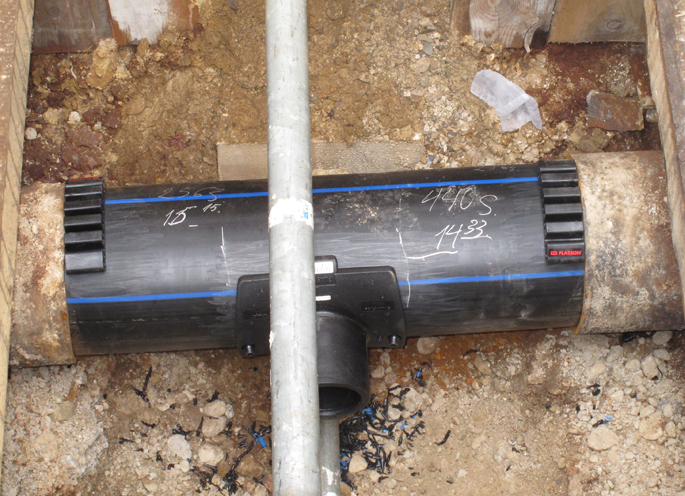
Bild 1: Links: PLASSON Flex-Fixierblock / Mitte: Anwendung Compact Pipe / Rechts: Anwendung U-Liner
Berlin: Die Ludwig Pfeiffer Hoch- und Tiefbau GmbH & Co. KG ist u.a. Spezialist für die Sanierung mit Close-Fit-Verfahren mit thermoplastischen Kunststoffrohren aus Polyethylen. Im Zuge der grabenlosen Erneuerung einer alten Abwasserdruckrohrleitung DN 1000 im Auftrag der Berliner Wasserbetriebe konnte nun erneut die wirtschaftliche und technische Leistungsfähigkeit dieser Sanierungstechnik unter Beweis gestellt werden. Um die gesamte Sanierungsmaßnahme in kürzester Zeit und mit minimaler Beeinträchtigung des Verkehrs, der Anwohner und der Umwelt durchzuführen, entschieden sich die verantwortlichen Akteure für den Einsatz des Close-Fit-Reduktionsverfahrens „DynTec“ der Ludwig Pfeiffer Hoch- und Tiefbau GmbH & Co. KG. Die Besonderheit des DynTec-Verfahrens liegt im Übermaß des PE-Liners gegenüber des Altrohres. Beim DynTec-Verfahren wird ein PE-HD Rohr mit Übermaß (DNNeurohr > DNAltrohr) mit konstanter Zugkraft durch ein Reduzierwerkzeug (konisches Gesenk) gezogen und der PE-Rohrstrang im elastischen Werkstoffbereich im Durchmesser um ca. 10 % reduziert, so dass der Einzug in das schadhafte Altrohr sichergestellt ist. Für den Einbau ist es erforderlich, in Abhängigkeit des zulässigen Biegeradius des PE-Rohres, der Tiefenlage des Altrohres sowie der erforderlichen Zugeinrichtung eine Start- und Zielbaugrube mit entsprechenden Widerlagern zu dimensionieren. Die Rückverformung des PE-Rohrstrangs nach dem Einzug findet nach vollständiger Reduzierung der Zugkraft an der Rohrleitung statt und garantiert so eine dauerhafte Close-Fit-Lage. Schließlich wird der PE-Rohrstrang in seiner Position fixiert und die Anbindung der Rohrenden an das weiterführende Leitungsnetz durchgeführt.
Leistungsfähigkeit des DynTec-Verfahrens beeindruckend
Im Zuge der Sanierung der alten Stahl-Abwasserdruckrohrleitung DN 1000 wurden durch die Ludwig Pfeiffer Hoch- und Tiefbau GmbH & Co. KG Kunststoffrohre aus PE-HD des Rohstofftyps PE 100 verbaut. Die Rohre in der Dimension dA 1020 x 60 mm (SDR 17) wurden als 12 m Stangenware zu einem PE-Rohrstrang mit einer Gesamtlänge von ca. 540 m auf Basis der Heizelementstumpfschweißtechnik gemäß DVS-Richtlinie 2207-1 miteinander verschweißt. Die bei der Heizelementstumpfschweißung entstehende Rohrinnen- und außenwulst in der jeweiligen Rohrverbindung wurde vollständig entfernt.
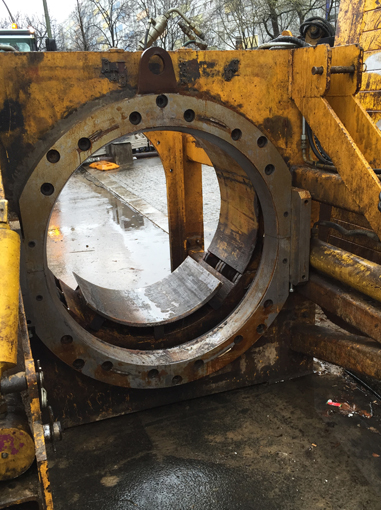
Bild 2: Konisches Gesenk
Der gesamte Rohrstrang wurde oberirdisch auf der Straße ausgelegt und auf Rollenböcken gelagert. Auf Basis der im Vorhinein durchgeführten Reinigung, TV-Untersuchung und Kalibrierung konnte eine ausreichende Vorbereitung des Altrohres und die Machbarkeit des Rohreinzugs sichergestellt werden. Über das am Zugkopf des PE-Rohrstrangs befestigte Zuggestänge erfolgte der Einzug in das Altrohr. Mit einer Zugkraft von ca. 170 Tonnen wurde der 540 m lange PE-Rohrstrang durch das konische Gesenk in das Altrohr eingezogen (Bild 2).
Die für den Einzugsvorgang notwendige Zugkraft wurde dabei ständig überwacht und sichergestellt, dass die maximal zulässige Zugbelastung für das Neurohr entsprechend DVGW Arbeitsblatt GW 320-1 nicht überschritten wurde. Der Einziehvorgang wurde mit einer Geschwindigkeit von ca. 40 bis 60 m pro Stunde durchgeführt und konnte nach einem Zeitraum von ca. 9 Stunden für den 540 m langen Rohrstrang erfolgreich abgeschlossen werden. Nach Erreichen der Endlage des Rohrstrangs wurde die Zugkraft langsam reduziert, so dass sich der Rohrstrang entspannte und sich der PE-Liner an die Rohrwandung des Altrohres anpresste.
Flex-Fixierblock bewährt sich im Praxiseinsatz
Ein weiterer wichtiger Arbeitsschritt zur Fertigstellung des Close-Fit-Liners bestand nun darin, den PE-Rohrstrang in seiner Position zu fixieren. In der praktischen Umsetzung entschieden sich die Ingenieure der Ludwig Pfeiffer Hoch- und Tiefbau GmbH & Co. KG für die Installation des PLASSON Flex-Fixierblocks. Ausschlaggebend hierfür waren die zulässige, definierte Kraftaufnahme sowie das sichere, schnelle und einfache Handling des Flex-Fixierblocks auf der Baustelle. Unter Berücksichtigung der zuvor ermittelten Gesamtfestpunktbelastung wurde für das Rohrende im Bereich der Zielbaugrube die Installation von 15 Stück Flex-Fixierblöcken festgelegt. Die Anordnung der Flex-Fixierblöcke auf dem Rohr erfolgte dabei über den Kreisumfang verteilt in gleichmäßigen Abständen. Der Außendurchmesser des PE-Rohrstrangs am Rohrende lag aufgrund der vorangegangenen Reduzierung mit ≤ dA 1000 mm im idealen Einsatzbereich des Flex-Fixierblocks, der den Nennweitenbereich von 160 bis 1600 mm stufenlos abdeckt.
Diese Flexibilität im Nennweitenbereich resultiert insbesondere aus der speziellen Rippenstruktur des Elektroschweißformteils. Zur Installation der Flex-Fixierblöcke wurde im ersten Arbeitsschritt die Oberfläche des PE-Rohres im Bereich der späteren Schweißzone lückenlos spanend bearbeitet. Sodann wurden die Schweißzone und die Formstückinnenseite jedes Flex-Fixierblocks mit einem PE-Reinigungsmittel gereinigt. Anschließend wurden die 15 Stück Flex-Fixierblöcke der Reihe nach auf einen Spanngurt aufgefädelt und der Spanngurt um das Rohr gelegt (Bild 3, links).
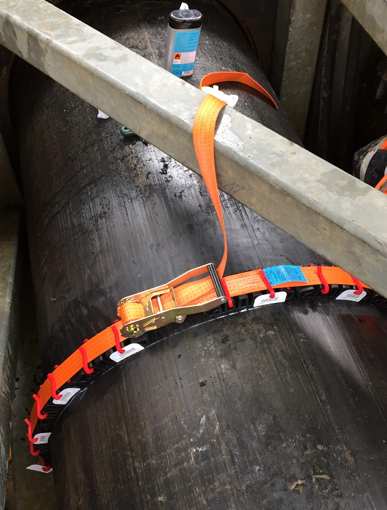
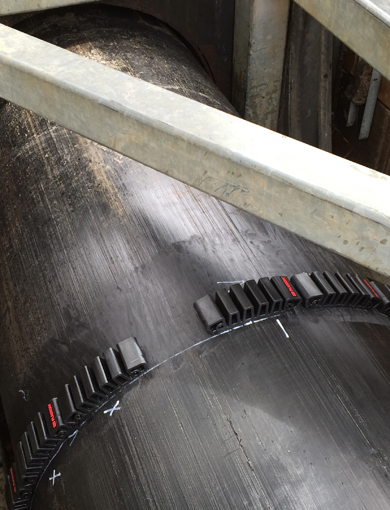
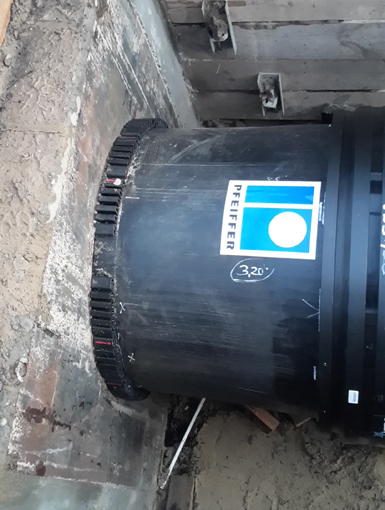
Bild 3: Links: PLASSON Flex-Fixierblock aufgefädelt/ Mitte: verschweißt/ Rechts: PE-Rohrstrang fixiert
Die fluchtgerechte Ausrichtung der Flex-Fixierblöcke wurde kontrolliert und der Spanngurt zur Fixierung der Festpunkte gespannt. Durch Einlesen des jeweils am Flex-Fixierblock angebrachten Barcodes wurde der Schweißvorgang ausgelöst und die Festpunkte nacheinander materialhomogen mit dem Rohr verschweißt (Bild 3, Mitte). Nach Einhaltung der vorgeschriebenen Abkühlzeit erfolgte die vollständige Entspannung des Rohrstrangs über die Zugeinrichtung. Dabei zog sich der PE-Rohrstrang bis zu den angebrachten Festpunkten bis zum Widerlager zurück (Bild 3, rechts). Die ebenfalls in der Startbaugrube durchgeführte Rohrendfixierung sorgte für die insgesamt längskraftschlüssige Ausbildung des gesamten PE-Rohrstrangs, so dass eine sichere Anbindung an das weiterführende Entwässerungsnetz gegeben war.
Fazit:
Close-Fit-Verfahren mit thermoplastischen Kunststoffrohren stellen eine wirtschaftliche und qualitativ hochwertige Alternative im Spektrum der grabenlosen Sanierungsverfahren dar. Insbesondere zur längskraftschlüssigen Ausbildung des eingezogenen PE-Rohres sowie zur Sicherung von Rohran- und verbindungen kommt der Auslegung, Auswahl und Anordnung von Festpunkten eine entscheidende Bedeutung zu.
Mit dem PLASSON Flex-Fixierblock steht dem Anwender nun ein Festpunkt als Elektroschweißformteil mit definierter Kraftaufnahme, flexiblem Einsatzbereich, sicherer, einfacher sowie schneller Installation und Verschweißung zur Verfügung. Sein zuverlässiger Einsatz bei PE-Rohren bei den Verformungs- und Reduktionsverfahren (z.B. Compact Pipe, U-Liner, DynTec) hat sich in der Praxis bewährt. Weitere Anwendungsmöglichkeiten ergeben sich beim Rohrstrang- und Einzelrohrverfahren bzw. überall dort, wo es gilt, PE-Rohre gegen Verschiebungen oder Bewegungen zu sichern.
- Flex-Fixierblock in PE 100 Material
- einsetzbar für PE Rohr mit dA 160 bis 1600 mm
- Verschweißung mit üblichen Elektroschweißgeräten
- verwendbare Rohrstofftypen: PE 80, PE 100 und PE 100 RC
- ausgelegt und geprüft zur Aufnahme von Kräften bis 31 kN pro Flex-Fixierblock
- durch Verwendung von mehreren Flex-Fixierblöcken sind höhere Kraftaufnahmen möglich
- einfache, schnelle und sichere Fixierung mittels Spanngurt durch angeordnete Halteklemmen
- weitere Anwendungsfälle: Einsatz als Auszugsicherung, z.B. PE-PVC Muffe; Reparatur mit nicht längskraftschlüssigen Kupplungen; zur Fixierung von Sinkgewichten